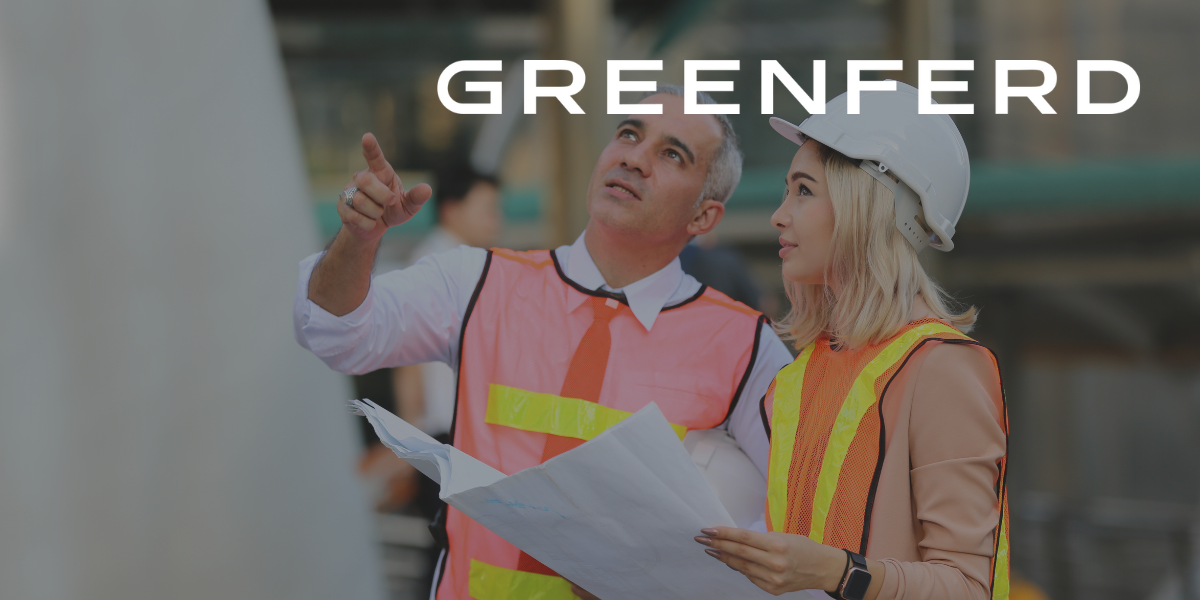
The Importance of Managing Deficiencies on a Commercial Construction Project
If you work in commercial construction, you are likely well acquainted with deficiencies – an industry term which is officially defined as a characteristic or condition that fails to meet a standard, or is not in compliance with a requirement or specification, in accordance with project expectations and requirements. Deficiencies are, unfortunately, an undeniable part of the commercial construction ecosystem; after all, commercial construction projects are complex undertakings that involve multiple stakeholders, timelines, and resources.
Even with meticulous planning and execution, it is not uncommon for deficiencies – which can range from minor defects to more significant challenges, such as material availability and supply-chain issues – to arise during the course of a project. However, if not proactively managed, deficiencies on a commercial construction project can become a costly and problematic challenge for key stakeholders with significant implications on the timeline, budget, and/or quality of a project.
At Greenferd, we understand that managing deficiencies on our projects requires a proactive approach that involves identifying, documenting, and addressing issues as soon as they arise. In this blog, we will discuss some of the key steps that we take to effectively manage and minimize deficiencies on all of our projects.
Hire Quality Trades
The success of any build is, in many ways, directly correlated with the quality of trades hired in the initial stages of the project. With this in mind, Greenferd operates with a simple but impactful core philosophy: the best way to effectively manage deficiencies is to exclusively work with the best trades in the industry. At the start of each project, we are careful to only solicit prices from trades who have a proven track record of success with us on projects of similar scope. More importantly, we select those trades who have proven effective at minimising the number of deficiencies in their work. By combining high trade standards with the diligence and experience of our site managers, our goal is to eliminate any deficiencies before they are even noted or identified on any deficiency list.
Establish a Deficiency Management Plan
The next step in managing deficiencies on our projects is to establish a ‘Deficiency Management Plan.’ This plan outlines the process for identifying, documenting, and addressing any deficiencies that arise over the course of the project. The plan also clearly defines the roles and responsibilities of each stakeholder involved in the deficiency management process, including the contractor, owner, architect, and any third-party consultants.
Conduct Regular Inspections
As the saying goes – you can’t manage what you can’t measure. With this in mind, regular inspections play an integral role in managing deficiencies. These inspections are conducted by our experienced team in partnership with professional consultants who are able to identify potential issues and document them in a formal deficiency report.
In an effort to keep this process more streamlined, the Greenferd team often uses technology to digitally identify any deficiencies which, in turn, ensures all stakeholders remain in the loop and can view and verify reported deficiencies. Our digital deficiency reports include a photo, a description of each deficiency, its severity, and its location, as well as the trade(s) responsible as well as any recommended remedial action.
Prioritize Deficiencies
Once deficiencies have been identified and documented, we prioritize them based on their perceived severity and impact to the project and the customer’s operations. Deficiencies that pose a safety risk or impact the functionality of the space should be addressed in a prioritized fashion, while minor cosmetic defects can be addressed at a more opportune time.
Assign Responsibility for Remediation
Each deficiency we identify is formally assigned to the appropriate trade(s) for remediation. Once assigned, the responsible parties are provided a clear timeframe to address the deficiency, in addition to the completion of any specific requirements for documentation or inspection of the remedial work.
Monitor Remediation
Once remediation work has begun, our team closely monitors progress to ensure that the deficiency has been appropriately addressed and resolved. The Greenferd team follows up with inspections, review documentation, and any other quality assurance measures we deem necessary to assure stakeholder satisfaction. If the remediation work is not satisfactory, additional action may be required, such as reassigning the task to a different trade or engaging a third-party consultant to provide additional oversight.
Document Remediation
Documentation is critical in managing deficiencies on a commercial construction project. With this in mind, all remediation work should be thoroughly documented, including a detailed log of all actions taken, any materials or equipment used, and any inspections or testing performed. This documentation should be maintained throughout the project and made available for review as needed.
Ultimately, managing deficiencies on our commercial construction projects requires a hands-on, proactive approach that includes a clear deficiency management plan, regular inspections, a deficiency prioritization system, a clear remediation plan, and thorough documentation of all remediation work. By following these steps, Greenferd ensures that deficiencies are managed effectively and their impact on the project timeline, budget, and quality is minimized to ensure the success of the project and, more importantly, the satisfaction of our client.
0 comments